Tube Fittings
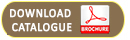
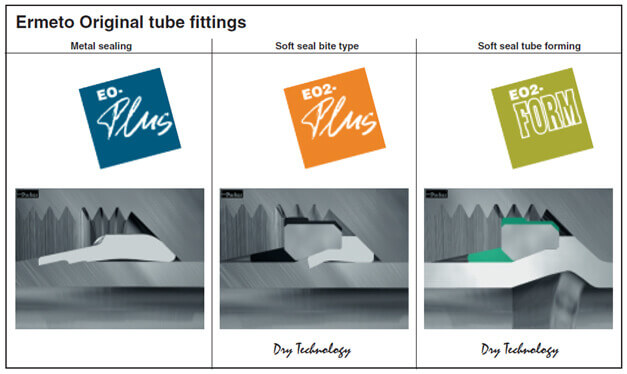
Introduction:
The bite type fitting was designed by Ermeto in Germany in the early 1930’s. Ermeto-fittings soon became popular due to the simple assembly which basically just requires two wrenches. Today, the EO fitting is the most widely used bite-type fitting in the world. EO fittings are designed for metric tube. All threads, hexagons, bores and other dimensions are purely metric. Historically it is based on German national standards 2353, DIN 3861, DIN 3859 and DIN 2353, which today are represented in the international standards ISO 8434. EO fittings are recognised for the high pressure performance from a compact body. EO fittings are available in the three series for low, medium and high pressures (LL, L and S-Series). This allows cost savings and -space minimized solutions for each specific application.
New Generation:
High performance tube fittings
The new, chromium6-free fitting generation from Parker Ermeto is called EO-Plus for metallic sealed connections, EO2-Plus for Dry Technology systems and EO2-FORM for formed tube soft-sealed systems without cutting rings. The new generation is characterised by maximum safety even under extreme pressures of up to 800 bar nominal pressure.
The further development of the proven Dry Technology EO-2 concept is designated EO2-Plus and gives extremely high pressure ratings and greatly reduced tightening torques for the larger fitting sizes. EO2-FORM is the new high pressure tube connection from Parker Ermeto. This concept unites the advantages of welded connections with those of EO-2 technology proven worldwide in millions of applications.
The New Generation from Parker Ermeto clearly exceeds the performance requirements of DIN/ISO standards: with its guaranteed 4-fold design factor, the new fitting generation can be used at the following nominal pressures in steel:
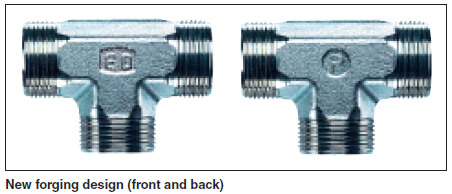
This extraordinary pressure and assembly performance can only be achieved by the use of even better and more resistant materials in combination with a special coating of individual components. This greatly extends the application range and the user does not have to sacrifice any advantages. Thanks to the higher pressure levels, less expensive “L” series fittings can now be used instead of the heavier “S” series.
The new multifunctional PSR cutting ring, the heart of the EO-Plus fitting, ensures a uniquely simple and easy assembly through its multifunctional ring geometry.
The new high performance forging design with its considerably larger flats size makes assembly even safer and easier. Through the application of a chromium6-free surface treatment, Parker Ermeto meets future requirements of the automotive industry today, and respects the directive of the European Parliament to eliminate the use of Chromium6. The removal of Chromium6 reflects Parker’s ongoing commitment to an environmentally clean and safe production process. The additional “Plus”: the corrosion resistance is increased to more than 500 hrs. to white rust.
The EO-LUB procedure is yet another innovation unique to Parker. In addition to the standard dry wax lubrication of the tube nuts, all larger fittings (25S/28L and above) are EO-LUB treated. EO-LUB reduces the assembly torques by approximately 25%, which makes assembly easier and prevents underassembly, the most common reason for bite-type tube fitting failure. This latest fitting generation benefits from Parker’s long years of experience combined with continuous innovation. It is made with our state-of-the-art production methods, controlled by the strictest quality assurance systems and procedures.
Enquiry
Triple-lok Fittings
Parker’s Triple-Lok 37° flare tube fittings have been used in industry since Mr. Parker pioneered the product in the 1930s. The 37° flare fitting is the most popular industrial tube/hose fitting connection in the world.
Today, Parker offers a broad range of Triple-Lok fittings meeting SAE J514, ISO 8434-2 and military standards and specifications.
The Triple-Lok design is quite simple. The tube fitting consists of three pieces: the body, the nut and the sleeve. The tube end is flared at a mating 37° angle and sandwiched between the fitting nose (seat) and the sleeve creating an effective seal between the fitting nose and tube flare or hose.
Parker’s Triple-Lok fittings are manufactured in steel, 316 stainless steel and brass for optimum fluid compatibility and corrosion resistance. Furthermore, available sizes range from 1/8" tube O.D. to 2" tube O.D. in several configurations. Adaptability to global ports is another key benefit of Triple-Lok. (Standard ports include: SAE, straight thread ISO-6149, NPT, BSPT, BSPP and DIN.)
The Triple-Lok tube fitting is also readily available for metric tubing and hose adapter applications. Simply by changing the industry standard sleeve, the same Triple-Lok body can be adapted to metric tubing in sizes ranging from 6 mm tube O.D. to 38 mm tube O.D. Likewise, by using only the body without the nut and sleeve, the Triple-Lok fitting is used as an industry standard hose adapter.
Parker’s Triple-Lok 37° flare tube fittings have been used in industry since Mr. Parker pioneered the product in the 1930s. The 37° flare fitting is the most popular industrial tube/hose fitting connection in the world.
Today, Parker offers a broad range of Triple-Lok fittings meeting SAE J514, ISO 8434-2 and military standards and specifications.
The Triple-Lok design is quite simple. The tube fitting consists of three pieces: the body, the nut and the sleeve. The tube end is flared at a mating 37° angle and sandwiched between the fitting nose (seat) and the sleeve creating an effective seal between the fitting nose and tube flare or hose.
Parker’s Triple-Lok fittings are manufactured in steel, 316 stainless steel and brass for optimum fluid compatibility and corrosion resistance. Furthermore, available sizes range from 1/8" tube O.D. to 2" tube O.D. in several configurations. Adaptability to global ports is another key benefit of Triple-Lok. (Standard ports include: SAE, straight thread ISO-6149, NPT, BSPT, BSPP and DIN.)
The Triple-Lok tube fitting is also readily available for metric tubing and hose adapter applications. Simply by changing the industry standard sleeve, the same Triple-Lok body can be adapted to metric tubing in sizes ranging from 6 mm tube O.D. to 38 mm tube O.D. Likewise, by using only the body without the nut and sleeve, the Triple-Lok fitting is used as an industry standard hose adapter.
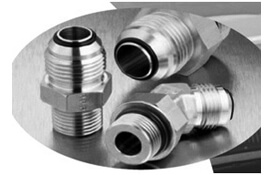
O-Lok Fittings
The Parker O-Lok fitting has been introduced to eliminate leakage in hydraulic systems and allow higher operating pressures (630 bar up to 12mm / 1/2" O.D.)
Parker O-Lok fittings in steel, stainless steel and brass are suitable for a wide range of tube dimensions and wall thicknesses. They are designed for use with metric and inch tubing.
A single Parker O-Lok fitting body can accommodate several different tube diameters just by changing the sleeve or braze-on spud.
Design and Construction
Parker O-Lok fittings can be assembled either by orbital 90° flanging of the tube using the Parker Parflange process or by brazing a spud on the tube end.
Flanging
Preparing the tube end using the Parker Parflange‚ process provides the user with the means of easily achieving a leak-free connection. It is ideal for in-house or on site applications.
Brazing
An alternative solution is to assemble Parker O-lok Fittings using a brazing spud on the tube end. Brazing can be useful for field assembly or when small quantities of tubes are being prepared.
EITHER CASE In both cases the tube end plus sleeve or spud acts as a reinforced point to provide higher vibration and impulse resistance. Parker O-Lok fittings consist of Fitting body, Sleeve, O-ring and Nut.
The Parker O-Lok Body There are over 30 different body shapes to choose from when specifying Parker O-Lok fittings for your application. The body face has a machined groove which contains an O-Ring. Parker O-Lok shape fittings are manufactured from forgings for greater strength and longer service life. The Parker O-ring A 90 degree Durometer Shore Nitrile O-ring is held captive in the groove of the fitting body. Note that Nitrile O-ring can be replaced by other O-ring materials.
Captive Groove Design
The O-ring groove incorporates an overhang to retain the O-ring in position, helping to eliminate O-ring loss or disturbance during tube assembly. This feature is now standardised under SAE J1453 as an alternative groove design.
The Parker O-Lok Sleeve
Mechanical sleeve
During the 90 degree flanging operation, the tube is pressed against the inner surface of the Parflange Sleeve, providing high rigidity when assembles to the fitting. Each Parflange sleeve is manufactured to strict tolerances and marker Parflanhe ensuring you of the highest quality assembly.
Brazed sleeve
Parker also manufacture spuds that can be brazed onto the tube. Reducing spuds allow Down sizing a large tube end to a smaller one.
The Parker O-Lok Nut
Parker O-Lok fitting nuts are cold formed (smaller sizes) or hot forged (larger sizes), depending on size.
Parker O-Lok Finish
Parker P-Lok steel fittings are yellow zinc plated (thickness 8 to 14um). This plating gives a high corrosion resistance (350 hours salt spray test to red rust*).
*Test in accordance with ASTM B117 or NFX 4.1.002.
Soft-Seal Capability
The design of the Parker O-Lok fittings used with the Parflange flanging system gives only one leak path which is sealed by a standard 90º Shore a Nitrile O-ring.
Reusability/Remake
Parker O-Lok fittings can be assembled and disassembled many times. It is recommended that the O-ring is replaced to ensure a perfect assembly.
The Parker O-Lok fitting has been introduced to eliminate leakage in hydraulic systems and allow higher operating pressures (630 bar up to 12mm / 1/2" O.D.)
Parker O-Lok fittings in steel, stainless steel and brass are suitable for a wide range of tube dimensions and wall thicknesses. They are designed for use with metric and inch tubing.
A single Parker O-Lok fitting body can accommodate several different tube diameters just by changing the sleeve or braze-on spud.
Design and Construction
Parker O-Lok fittings can be assembled either by orbital 90° flanging of the tube using the Parker Parflange process or by brazing a spud on the tube end.
Flanging
Preparing the tube end using the Parker Parflange‚ process provides the user with the means of easily achieving a leak-free connection. It is ideal for in-house or on site applications.
Brazing
An alternative solution is to assemble Parker O-lok Fittings using a brazing spud on the tube end. Brazing can be useful for field assembly or when small quantities of tubes are being prepared.
EITHER CASE In both cases the tube end plus sleeve or spud acts as a reinforced point to provide higher vibration and impulse resistance. Parker O-Lok fittings consist of Fitting body, Sleeve, O-ring and Nut.
The Parker O-Lok Body There are over 30 different body shapes to choose from when specifying Parker O-Lok fittings for your application. The body face has a machined groove which contains an O-Ring. Parker O-Lok shape fittings are manufactured from forgings for greater strength and longer service life. The Parker O-ring A 90 degree Durometer Shore Nitrile O-ring is held captive in the groove of the fitting body. Note that Nitrile O-ring can be replaced by other O-ring materials.
Captive Groove Design
The O-ring groove incorporates an overhang to retain the O-ring in position, helping to eliminate O-ring loss or disturbance during tube assembly. This feature is now standardised under SAE J1453 as an alternative groove design.
The Parker O-Lok Sleeve
Mechanical sleeve
During the 90 degree flanging operation, the tube is pressed against the inner surface of the Parflange Sleeve, providing high rigidity when assembles to the fitting. Each Parflange sleeve is manufactured to strict tolerances and marker Parflanhe ensuring you of the highest quality assembly.
Brazed sleeve
Parker also manufacture spuds that can be brazed onto the tube. Reducing spuds allow Down sizing a large tube end to a smaller one.
The Parker O-Lok Nut
Parker O-Lok fitting nuts are cold formed (smaller sizes) or hot forged (larger sizes), depending on size.
Parker O-Lok Finish
Parker P-Lok steel fittings are yellow zinc plated (thickness 8 to 14um). This plating gives a high corrosion resistance (350 hours salt spray test to red rust*).
*Test in accordance with ASTM B117 or NFX 4.1.002.
Soft-Seal Capability
The design of the Parker O-Lok fittings used with the Parflange flanging system gives only one leak path which is sealed by a standard 90º Shore a Nitrile O-ring.
Reusability/Remake
Parker O-Lok fittings can be assembled and disassembled many times. It is recommended that the O-ring is replaced to ensure a perfect assembly.
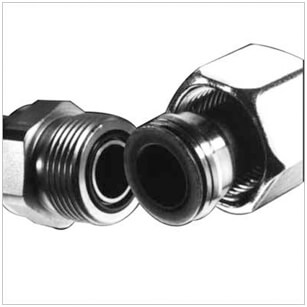
EO2 FORM
EO2-FORM is the new high pressure formed tube Generation of the Tube Fittings Division Europe. As with EO2- Plus, it is designed in to eliminate leakage in all fluid systems, by using elastomeric sealing systems.
The common feature of all EO2-FORM connections are the EO2 seal elements (Dry Technology) as well as the new cold forming process, that gives extreme rigidity and low tightening torques. The seals are now also available in FKM (e.g. Viton®) for applications with higher temperatures or aggressive media. Through EO2-FORM, elastomeric sealing technology is made available even where bite-type connectors are not popular, like in hydraulic presses, cranes, lifts or ship canal locks. Compared to welding or brazing, the EO2-FORM process is faster and easier. It does not require special tube treatment, heating or chemicals. EO2-FORM is designed for metric tube and fully interchangeable to the complete Ermeto Original product range according to ISO 8434-1 / DIN 2353. EO2-FORM is available in “L”- and “S”-Series.
Function of EO2-FORM
EO2-FORM is not a stand-alone product. It has been developed as an extension of the proven EO2-Plus system product range. All EO2-FORM components like nuts, seals and fitting bodies come from the EO2-Plus program. The only investment needed is the forming machine, which pays off quickly as it reduces assembly time and effort. Assembly characteristics of EO2-FORM are similar to EO2-Plus too. This allows the customer to use both products for his hydraulic pipework without increasing stock or confusing workfloor engineers with new components.
Elastomeric sealing
For EO2-FORM, the same sealing ring “DOZ” is used as for EO2-Plus. The high volume elastomeric seal assures a hermetically sealed tube joint. It is located in between the inner cone of the fitting body and the tube surface, thus blocking the only possible leak path. Due to its large cross section, the seal effectively compensates for all manufacturing tolerances between the tube and fitting cone. The sealing effect is pressure supported which makes the EO2-FORM fitting ideal for high pressure applications. The static compression also eliminates air-ingress into the fluid system in vacuum conditions.
Elastomerically sealed EO2-FORM fittings do not require any retightening even in heavy-duty applications. Seal extrusion is prevented by proper housing without gaps or dead volume areas. The sealing lip is bonded to a metallic support ring.
Cold-formed tube
The cold-forming of the tube is carried out by the EO2-FORM machine. Machine operation and tool setup are optimised for short cycle times, which makes the process easy and fast. The tube is connected when the sealing ring is fixed and the nut is tightened. The working contact area of the EO2-FORM connection is the flat front surface of the metallic support ring which is made of heat-treated, high-strength steel. This provides superior mechanical strength without settling, loosening or need for re-tightening.
EO2-FORM is the new high pressure formed tube Generation of the Tube Fittings Division Europe. As with EO2- Plus, it is designed in to eliminate leakage in all fluid systems, by using elastomeric sealing systems.
The common feature of all EO2-FORM connections are the EO2 seal elements (Dry Technology) as well as the new cold forming process, that gives extreme rigidity and low tightening torques. The seals are now also available in FKM (e.g. Viton®) for applications with higher temperatures or aggressive media. Through EO2-FORM, elastomeric sealing technology is made available even where bite-type connectors are not popular, like in hydraulic presses, cranes, lifts or ship canal locks. Compared to welding or brazing, the EO2-FORM process is faster and easier. It does not require special tube treatment, heating or chemicals. EO2-FORM is designed for metric tube and fully interchangeable to the complete Ermeto Original product range according to ISO 8434-1 / DIN 2353. EO2-FORM is available in “L”- and “S”-Series.
Function of EO2-FORM
EO2-FORM is not a stand-alone product. It has been developed as an extension of the proven EO2-Plus system product range. All EO2-FORM components like nuts, seals and fitting bodies come from the EO2-Plus program. The only investment needed is the forming machine, which pays off quickly as it reduces assembly time and effort. Assembly characteristics of EO2-FORM are similar to EO2-Plus too. This allows the customer to use both products for his hydraulic pipework without increasing stock or confusing workfloor engineers with new components.
Elastomeric sealing
For EO2-FORM, the same sealing ring “DOZ” is used as for EO2-Plus. The high volume elastomeric seal assures a hermetically sealed tube joint. It is located in between the inner cone of the fitting body and the tube surface, thus blocking the only possible leak path. Due to its large cross section, the seal effectively compensates for all manufacturing tolerances between the tube and fitting cone. The sealing effect is pressure supported which makes the EO2-FORM fitting ideal for high pressure applications. The static compression also eliminates air-ingress into the fluid system in vacuum conditions.
Elastomerically sealed EO2-FORM fittings do not require any retightening even in heavy-duty applications. Seal extrusion is prevented by proper housing without gaps or dead volume areas. The sealing lip is bonded to a metallic support ring.
![]() |
![]() |
Cold-formed tube
The cold-forming of the tube is carried out by the EO2-FORM machine. Machine operation and tool setup are optimised for short cycle times, which makes the process easy and fast. The tube is connected when the sealing ring is fixed and the nut is tightened. The working contact area of the EO2-FORM connection is the flat front surface of the metallic support ring which is made of heat-treated, high-strength steel. This provides superior mechanical strength without settling, loosening or need for re-tightening.
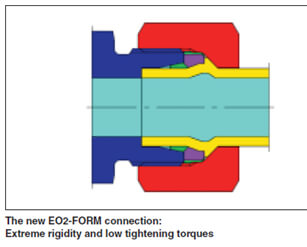
EO2 PLUS
The original fitting system used worldwide in millions of applications is now available in a new design: more safety even under the highest pressure, chromium6-free surface treatment with significantly higher corrosion resistance, and considerably reduced tightening torques.
The ingenious invention of the cutting ring fitting was made by the founder of Parker Ermeto in the late nineteen twenties. In 1934, this idea was patented and today it is just as useful as it was on the very first day. Considering the range of applications, quality, reliability and functional safety, the principle of the Parker’s cutting ring fitting has been a leading system up to today. Of course, this has only been possible by continuously adapting the original invention from 1934 to the practical requirements of state of the art technology. Thus, the first Parker Ermeto cutting ring has little left in common with the latest multifunctional PSR cutting ring, the heart of EOPlus.
The EO-Plus fitting meets the requirements of modern hydraulic systems. This is especially true for applications where the systems are exposed to extremely high loads. EO-Plus is designed for metric tube and based on German Standards DIN 3861 and DIN 2353, which today are represented by the international standard ISO 8434-1. EO-Plus is available in “L”- and “S”-Series.
The PSR (Progressive Stop Ring) is available for the steel fitting range. For stainless steel applications, the Progressive ring DPR 71 is used and the Cutting ring for brass fittings and series LL.
EO-Plus fitting features
The EO-Plus fitting produces high pressure, leak free connection of tubes and components in fluid systems. The basic function of EO-Plus is the controlled progressive bite of the PSR into the tube due to a unique internal geometry.
The front cutting edge A has already started cutting into the tube before the second cutting edge B begins. As soon as both cutting edges have cut into the tube to the designed depth further advance is limited by the stop shape C and the new overtightening protection D. Additionally, the special form of the PSR with its dimples at the front shoulder section gives an assembly state control.
Owing to the design of both cutting edges and stop shape all forces arising are equally distributed. This distribution along with the specially designed interior collar E of the ring guarantees increased safety, particularly with regard to vibration and flexure stresses. Service vibration loading is not present in the areas of the tubing where the bite is made.
The stop shape as well as the overtightening protection cause a clear sharp increase in tightening forces. After assembly, a visible collar F of cut tube material must completely fill the space in front of the first cutting edge. A slight bowing up of the ring G is desirable. This spring effect provides permanent compensation for flexural vibration and settling effects in the thread of the fitting nuts.
The original fitting system used worldwide in millions of applications is now available in a new design: more safety even under the highest pressure, chromium6-free surface treatment with significantly higher corrosion resistance, and considerably reduced tightening torques.
The ingenious invention of the cutting ring fitting was made by the founder of Parker Ermeto in the late nineteen twenties. In 1934, this idea was patented and today it is just as useful as it was on the very first day. Considering the range of applications, quality, reliability and functional safety, the principle of the Parker’s cutting ring fitting has been a leading system up to today. Of course, this has only been possible by continuously adapting the original invention from 1934 to the practical requirements of state of the art technology. Thus, the first Parker Ermeto cutting ring has little left in common with the latest multifunctional PSR cutting ring, the heart of EOPlus.
![]() |
![]() |
The EO-Plus fitting meets the requirements of modern hydraulic systems. This is especially true for applications where the systems are exposed to extremely high loads. EO-Plus is designed for metric tube and based on German Standards DIN 3861 and DIN 2353, which today are represented by the international standard ISO 8434-1. EO-Plus is available in “L”- and “S”-Series.
The PSR (Progressive Stop Ring) is available for the steel fitting range. For stainless steel applications, the Progressive ring DPR 71 is used and the Cutting ring for brass fittings and series LL.
EO-Plus fitting features
The EO-Plus fitting produces high pressure, leak free connection of tubes and components in fluid systems. The basic function of EO-Plus is the controlled progressive bite of the PSR into the tube due to a unique internal geometry.
The front cutting edge A has already started cutting into the tube before the second cutting edge B begins. As soon as both cutting edges have cut into the tube to the designed depth further advance is limited by the stop shape C and the new overtightening protection D. Additionally, the special form of the PSR with its dimples at the front shoulder section gives an assembly state control.
Owing to the design of both cutting edges and stop shape all forces arising are equally distributed. This distribution along with the specially designed interior collar E of the ring guarantees increased safety, particularly with regard to vibration and flexure stresses. Service vibration loading is not present in the areas of the tubing where the bite is made.
The stop shape as well as the overtightening protection cause a clear sharp increase in tightening forces. After assembly, a visible collar F of cut tube material must completely fill the space in front of the first cutting edge. A slight bowing up of the ring G is desirable. This spring effect provides permanent compensation for flexural vibration and settling effects in the thread of the fitting nuts.
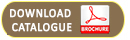